25º abr. 2013
Many of today’s automotive axle-makers are removing cost from their manufacturing processes by welding ring gears to their assemblies. This growing approach makes new demands on the bevel gear rolling test machine, and Gleason’s 360T Universal Gear Tester is keeping pace with the right solutions.
Among these is a unique and robust tailstock unit, a critical system for these gear-makers. The tailstock is compatible with 90 degree and angular bevel gear-sets and functions with all the advanced measurements offered by the machine—SFT (Single Flank Test), SBN (Structure-Borne Noise), searches, sweeps, etc.
In the conventional process, a ring gear is bolted to its differential-case assembly, which typically requires 8 or more blind tapped holes to be prepared in the blank. During the fastening process, the gear is reliably positioned and is not distorted in a significant way. Therefore, it is normally sufficient and easiest to roll test the loose ring gear with its mating pinion to verify running quality prior to the assembly process. A loose ring gear can be clamped very stiffly and securely with conventional fixtures such as Gleason Uni-Spand™ or X-Pandisk™ tooling, since the gear can be well supported by its bore and back seating surface.
In the newer alternative process the hardened, finished gear is pressed onto the assembly and welded in place. In such cases, the gear can be distorted in known ways (that the manufacturer accounts for), or it could occasionally be mis-positioned by the automated welding process. Therefore, it is no longer sufficient—or in some cases even possible—to verify gear set quality by roll testing at the loose ring gear stage.
So, it is necessary to clamp the complete gear-on-dif-case assembly in the production test machine. This creates a support issue since the surfaces available for clamping the assembly from the “in-board” (gear spindle) side are much diminished. These surfaces usually comprise a short, small-diameter bearing journal and a small axial seating ring. Attempting to align and support the assembly by colleting just these surfaces can be a problem, especially when the ring gear is overhanging (mounted a considerable distance away.)
Although various “outboard support” devices have been available on roll testers for many years, they have all been relatively weak structurally. Their role has thus been limited to assistance with alignment during initial clamping, but they have done little to support the part during testing. Today’s gear makers often prescribe moderate-to-high test loads and speeds where proper support is imperative. A true tailstock spindle, robustly connected to the machine structure, is required to support the part securely and to better represent the stiffness the gear set experiences in the final application.
Such a tailstock has been developed as an optional but integrated part of the 360T test machine, and offers unrivalled mounting stiffness. Whether supporting the part on a center cone, or colleting on an outboard journal, this spindle—together with inboard clamping from the main spindle—provides both the alignment and stiffness needed to properly support today’s range of gear-on-dif-case testing. The hydraulically-controlled unit engages and disengages the part automatically.
Use of the tailstock has proven crucial for gear-makers to achieve their quality-control goals for up-front roll testing and to get correlation with end-of-line axle and vehicle testing. The tailstock system is fully production ready—fast and efficient whether testing 100% or sampling
With or without the tailstock, the 360T is the world’s only fully-CNC angular gear tester. It is capable of both bevel and cylindrical testing, and today serves automotive, truck, industrial, and aircraft markets around the world. The tailstock is just one of many unique class-leading features and options on the machine, which include pinion height probing, arbor run-out cancellation, and the incredible cycle time savings of overlapping continuous searches. The machine is also available in a 90 degree only version.
Please contact Gleason Sales for more information on the 360T or its tailstock capability. We’d be happy to review your applications and recommend solutions that meet your needs today and tomorrow.
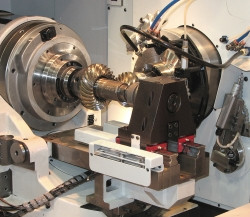